What is Galvanising?
When talking about galvanisation in the metal industry, this usually refers to the application of a thin layer of zinc on metal. This process is also called galvanising or electrolytic galvanizing. The purpose of this is to prevent corrosion and, for example, to offer roll containers, stillages or stacking racks a longer life. However, in addition to electrolysis and zinc, other options and materials are also available to extend the life of metal. Hot-dip galvanising, for example, is an excellent (and sometimes better) alternative.
In previous blogs about roll containers and stacking racks, we have already briefly explained the definition of electroplating, hot-dip galvanizing and other related terms. However, electroplating is a complex process that we would like to discuss in more detail. Read below all the facts about electroplating, galvanizing and electrolysis based on practical examples. Some examples of hot-dip or electrolytically galvanized products from our webshop:
What is electroplating and how does it work?
Electroplating is a process in which a thin layer of metal is applied to a product, also known as a workpiece. Usually, this workpiece is mostly made of iron and the purpose of electroplating is to prevent corrosion to counteract. Think, for example, of applying a thin layer of zinc to the iron walls of a roll container so that it does not rust when it gets wet. The weathering process is postponed as much as possible, which extends the life of the product. There is no deformation of the workpiece with electroplating because the bath only reaches 30 to 70°C. This is too low a temperature to deform iron. The layer thickness of the material to be applied can be determined quite precisely and ranges from 5 to 40 micrometers (µm). This is quite thin and post-processing to remove any burr edges that have arisen during the bonding process is usually not necessary.
What is electrolytic galvanizing?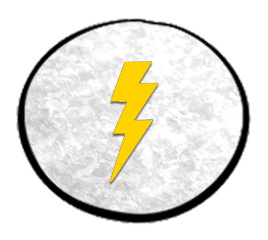
Electroplating in which zinc is used to protect the object is also known as electrolytic galvanizing. Use is made here of the so-called Galvano technique on which the word galvanisation is based. The terms electroplating and galvanising are often confused because they are not mutually exclusive. To avoid confusion, it is better to use the precise term electrolytic galvanising. The electroplating technique involves more than just galvanising. For example, one can also refer to the chrome plating or nickel plating of iron.
Many Rotomshop products such as roll containers are electrolytically galvanised because they are (occasionally) also used outdoors. In addition, it leads to a beautiful, glossy finish that can also be used in consumer / customer environments. Metal Pallet Converters are, for example, widely used in retail stores to offer grab stock or to be able to place offers outside the fixed racks.
What is hot-dip galvanising?
The process of hot-dip galvanising is drastically different from electrolytic galvanising. The temperature of the zinc bath is about 450°C, so that the zinc layer and the iron fuse to form a very strong alloy. The layer thickness of hot-dip galvanising is 30 to 200 micrometers (µm). The thickness of the zinc layer depends on factors such as the speed at which the product is removed from the zinc bath and the temperature. Hot-dip galvanising thus results in a thicker layer than electrolytic galvanising and offers better protection against corrosion. A second advantage is that hollow spaces can also be reached if the treated product is provided with air holes (and therefore does not contain closed spaces) and outlet holes.
A disadvantage of hot-dip galvanising is that some post-processing is often necessary. The heat can cause certain parts to twist or deform slightly. In addition, solidified drops of zinc must be removed and any threads and holes cleaned to achieve the desired result without burrs. Hot-dip galvanised products usually have a matte grey finish. Think, for example, of lampposts and crash barriers. The difference in finish and appearance between hot-dip galvanising and electrolytic galvanising is clearly visible below.
And which method of galvanizing best for me?
Do you occasionally use your products outside and do they only occasionally get wet or damp? Then electrolytic galvanisation - one way of galvanizing - offers your product sufficient protection against corrosion. An additional advantage is that this treatment usually has a smoother and more beautiful finish and is usually less expensive than hot dip galvanising. Handy if you want to be able to use your electrolytically galvanised roll containers without gloves on.
You may often use your products such as roll containers or stacking racks in wet environments and there may be a need for more scratch and impact resistance. In that case, opt for hot-dip galvanising. Although this treatment is the most expensive, it offers the best protection against corrosion and therefore your products will last longer. Our stacking racks are a good example of this. These are standard equipped with hot-dip galvanizing because they are often used outdoors and must be able to withstand a knock.
We can conclude that the treatment methods of electrolytic and hot-dip galvanising both add a lot to products with a high iron content that are used outdoors - whether or not very frequently. Many of our products therefore already state whether they have been treated and how this was done exactly. That way you never miss a thing and you know where you stand!
Questions about this blog regarding electroplating or questions about other processes and load carriers of Rotomshop? Contact us via [email protected] or 01777 322100.